Master Builders Solutions
Project Atlas
Empowering concrete producers with real-time data
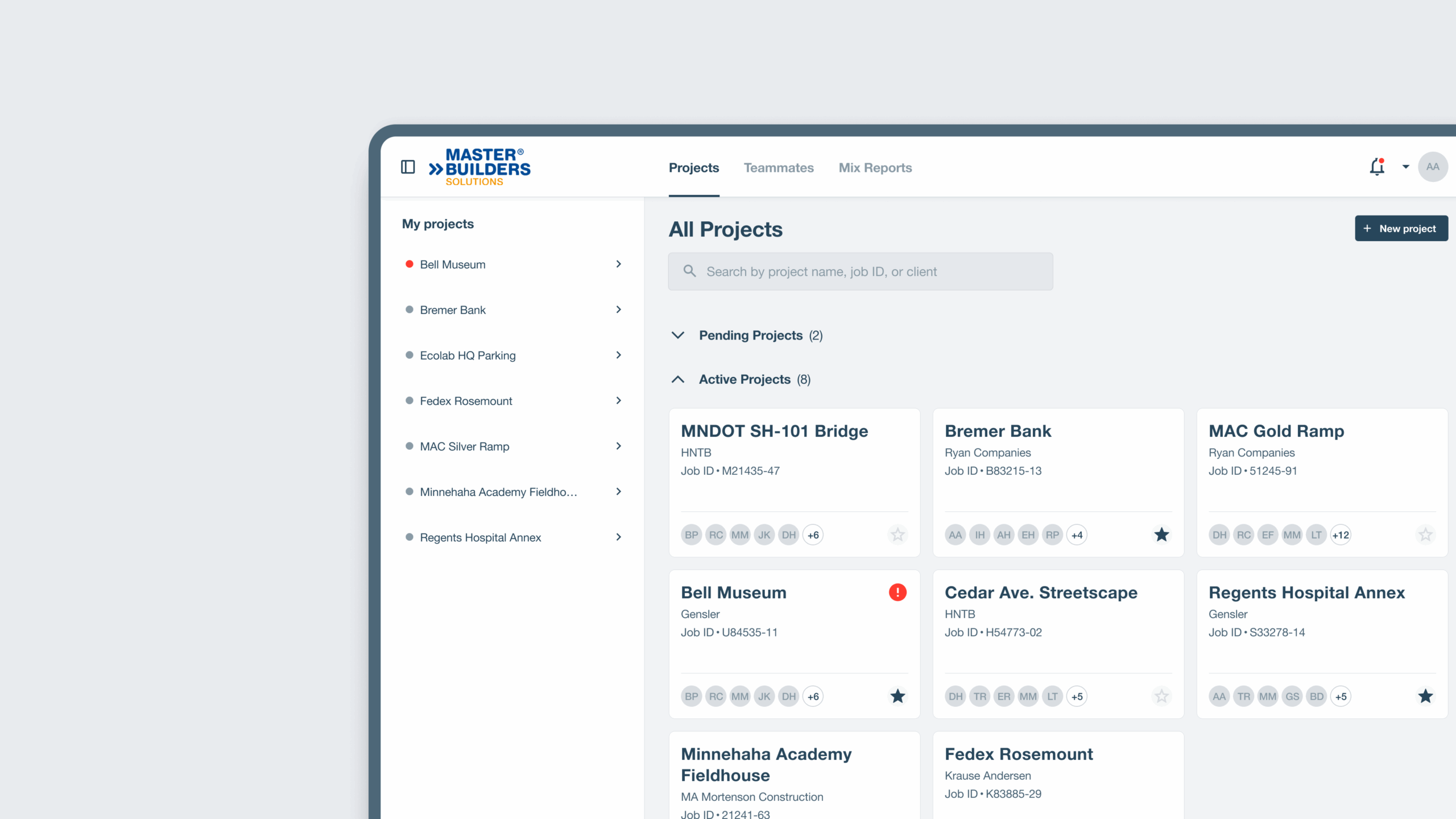
Project Atlas was a product innovation effort aimed at providing ready mix producers with the real-time data and actionable insights needed to maintain the highest-quality concrete from plant to job site.
Immersion
To gain a thorough understanding readymix industry, all stages were explored with the concrete experts from Master Builder Solutions through a series of discovery workshops
The entire journey, spanning job estimation to post-delivery operations, was documented in the form of a touchpoint map providing a clear visualization of roles and responsibilities throughout the product lifecycle, enabling the team to discuss process gaps and areas in need of improvement.
These sessions prioritized the need to address the challenges associated with maintaining predictable concrete loads during the critical journey from the plant to the job site.
In addition to the main goal, the project uncovered a secondary focus: collecting batch data to optimize future mix designs.
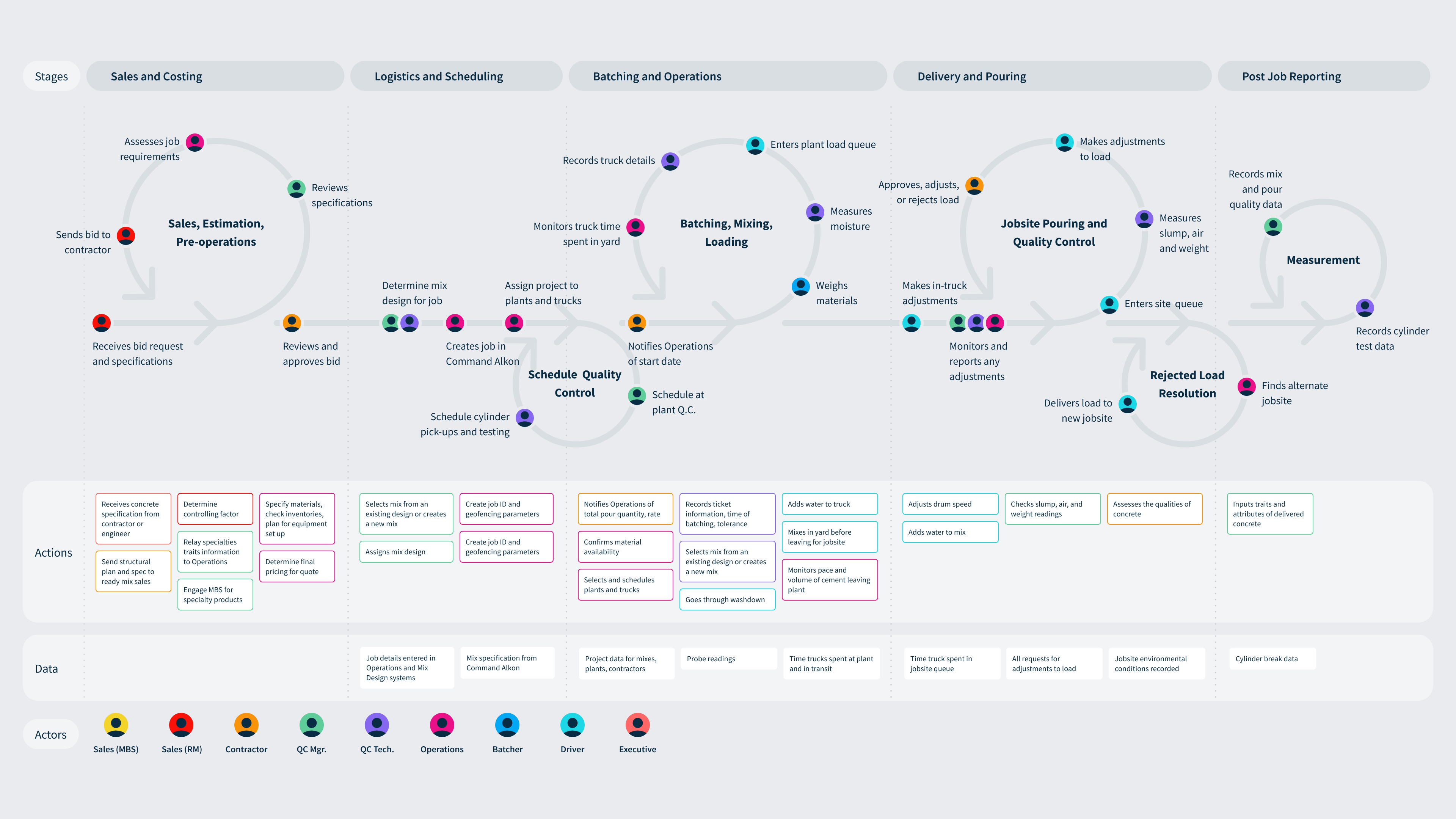
Touchpoint map identifying the people, processes, data sources, and the challenges of poured concrete jobs.
Problem Definition
Through in-depth interviews with ready-mix producers, dispatchers, and quality control personnel, three critical areas, plagued with recurring pain points and gaps, were identified.
Lack of Real-time Data
Concrete producers are tasked with managing a multitude of variables, such as material availability, environmental conditions, and travel times. However, they lack access to real-time data, hindering their ability to make informed decisions and respond promptly to changing circumstances.
Inefficient Communication Channels
Communication between different disciplines and team members often suffers from inefficiencies, leading to miscommunications, delays, cost overruns, and even rejected concrete. Enhancing communication channels emerged as an area for improvement.
Quality Control Challenges
Quality control personnel face increasing complexity in adhering to stringent specifications and sustainability requirements. This challenge demands close attention to detail to ensure consistent quality while maintaining profitability.
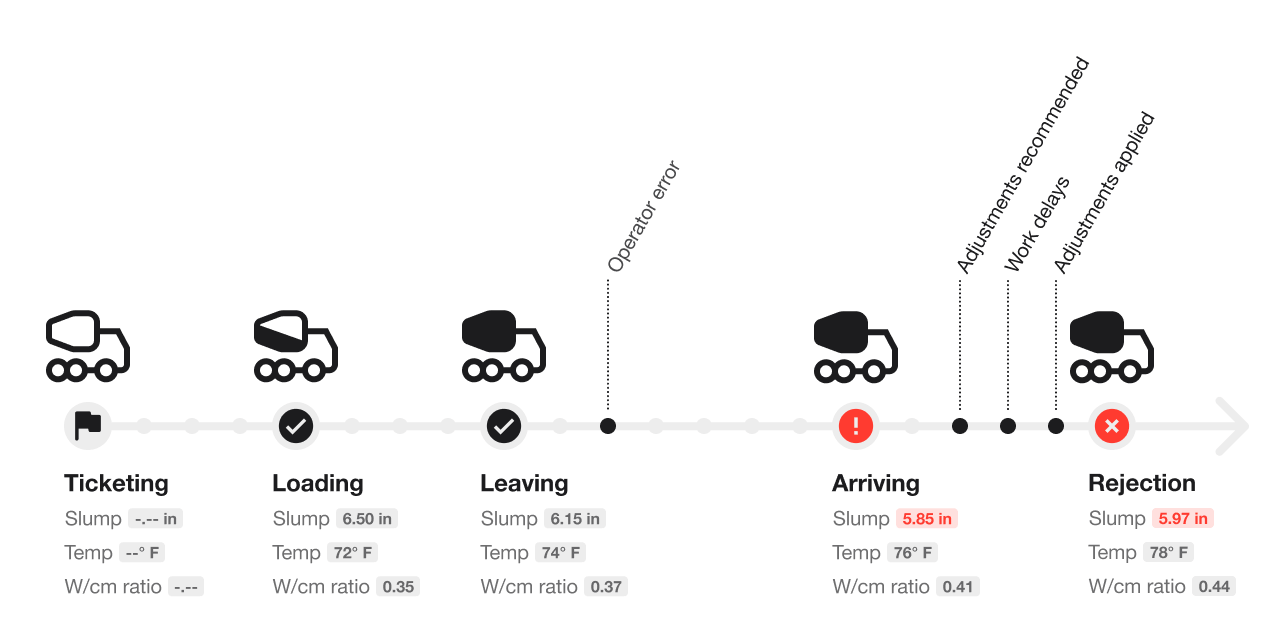
Insights & Work
Integrating real-time data from sensors (at plants, in trucks, and on jobsites) into a single platform empowers team members in critical decision-making moments to assure the integrity of delivered concrete.
Through work with quality control managers, we identified the details they use in traditional paper tickets as well as ones needed for monitoring batch quality from plant to job site.
With this information, I worked with operations and materials experts to write user stories for scenarios that could utilize data from the sensors recording material and environmental data, the roles and responsibilities of team members, the risks to concrete quality, and any corrective actions that may be taken to maintain mix integrity during its journey from plant to pour site.
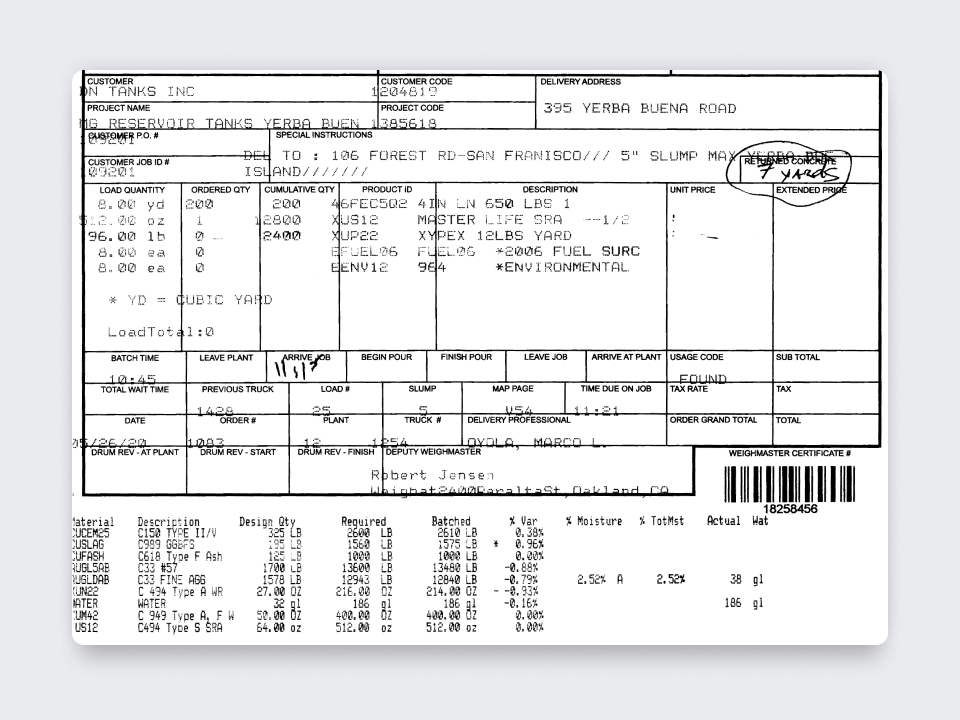
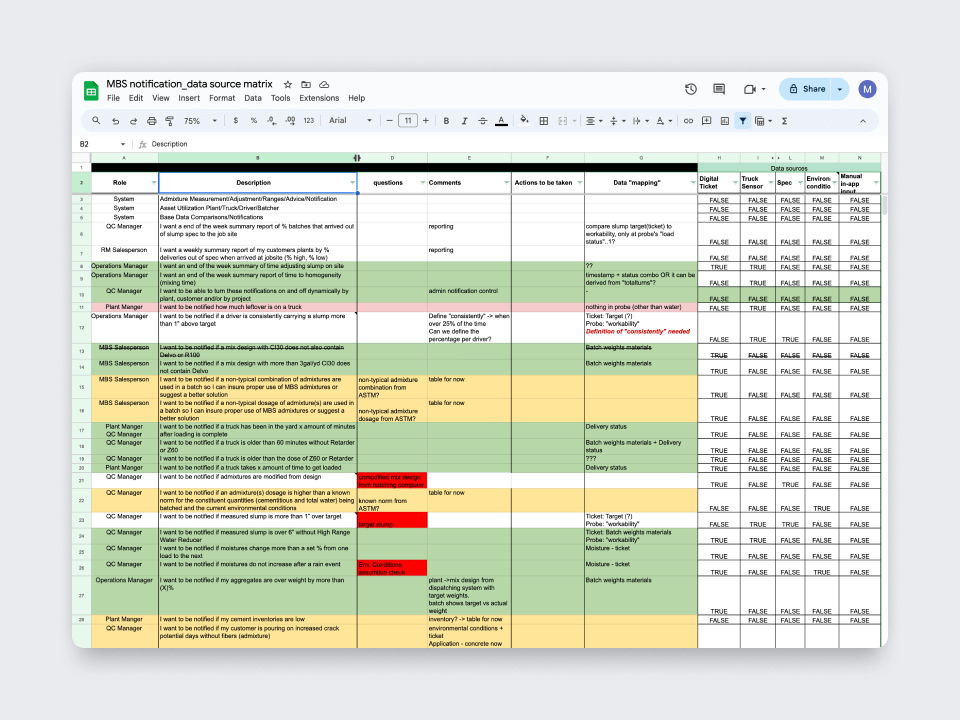
By notifying the right people at the right time when an outlier is detected, decision-makers have time to analyze the situation, identify the cause, and take action to resolve the issue.
Data analysts, engineers, and third-party partners evaluated the user stories to ensure the system architecture delivers appropriate updates to the right team members at the right times, delivering high-quality concrete to the job site.
Early concept tests showed no single solution for delivering pertinent information to the right person in every scenario. Operations managers now configure teams and alerts on a project-by-project basis, ensuring a solution aligns with each project’s unique requirements.
When an out-of-range material parameter is detected, alerts promptly push to qualified team members, detailing the issue and preceding events. These team members are empowered to take action, triggering notifications that provide a record of their actions and inform them of the next steps.
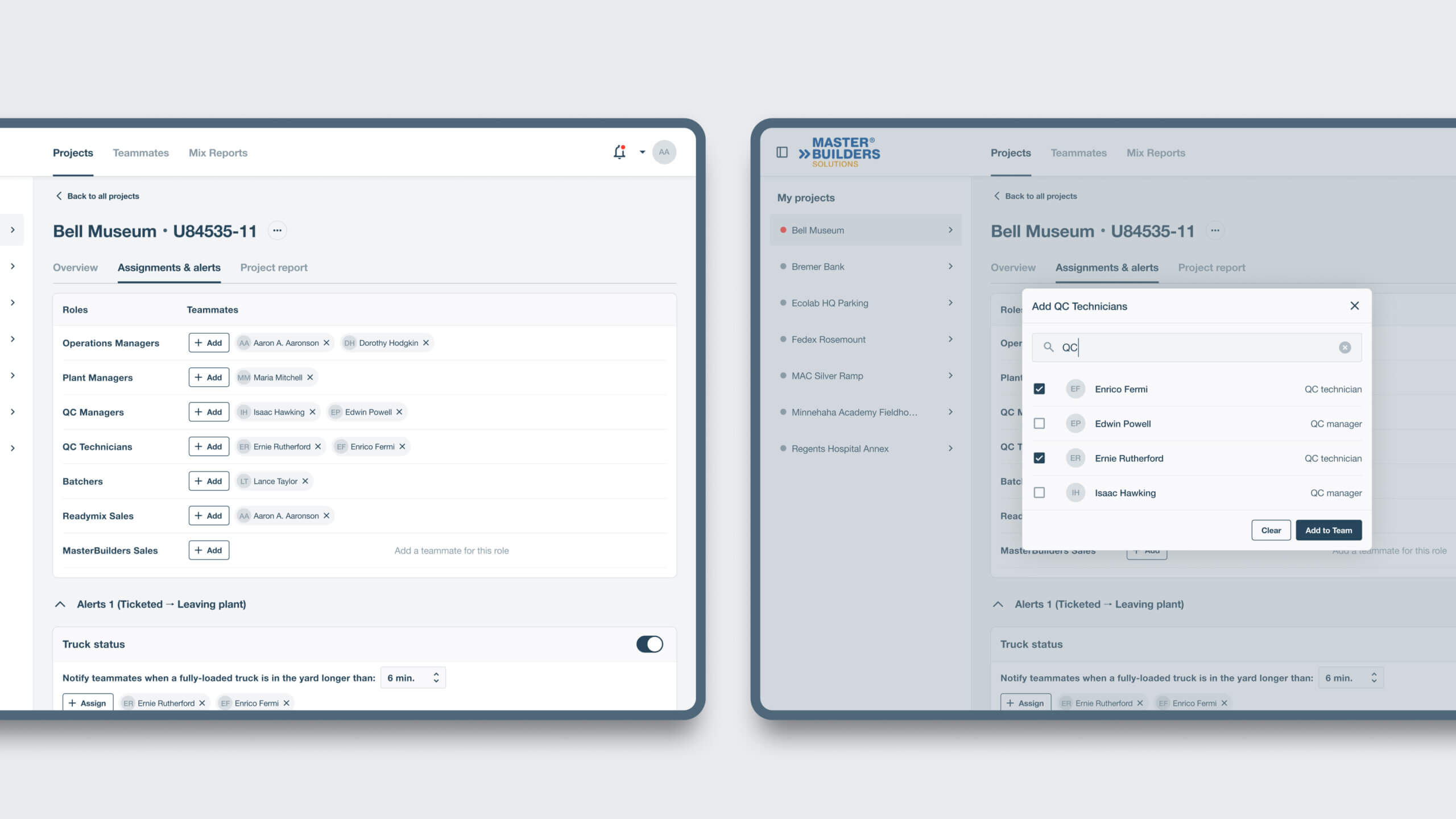
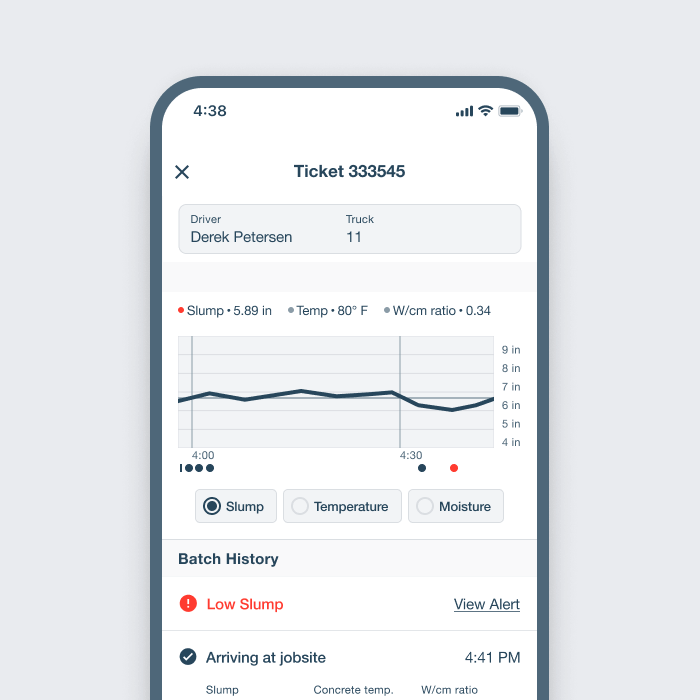
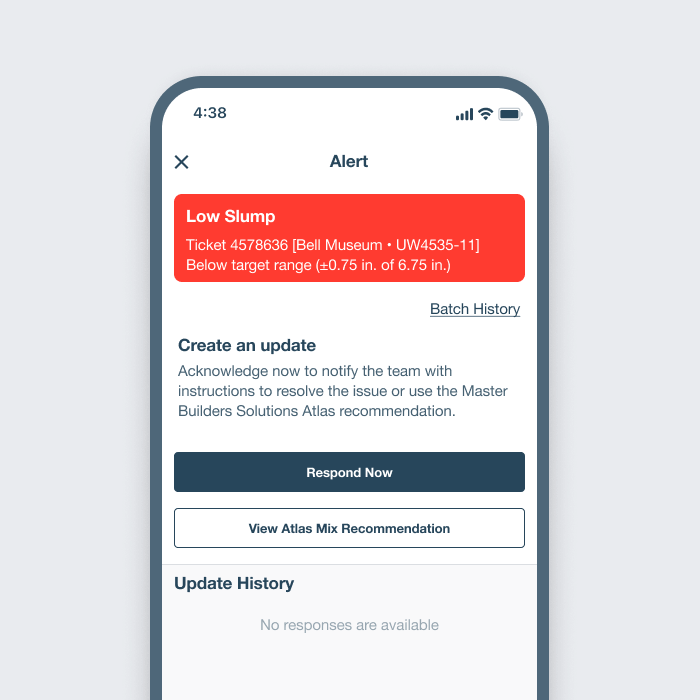
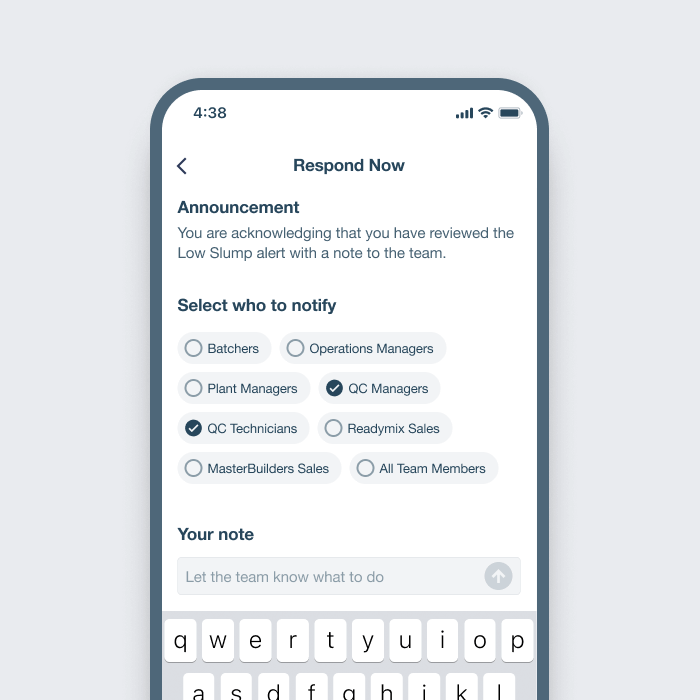
Capturing better project and batch data helps to ensure future projects face fewer risks to material quality while maximizing margins.
Using data collected from our new tracking system, we designed the administrator portal to seamlessly consolidate delivery histories with a library of mix specifications. This empowers ready mix producers with the ability to see implementation track records for each of their mix designs. This integrated approach enables proactive measures to be taken, leveraging historical data and insights to improve outcomes in future jobs.
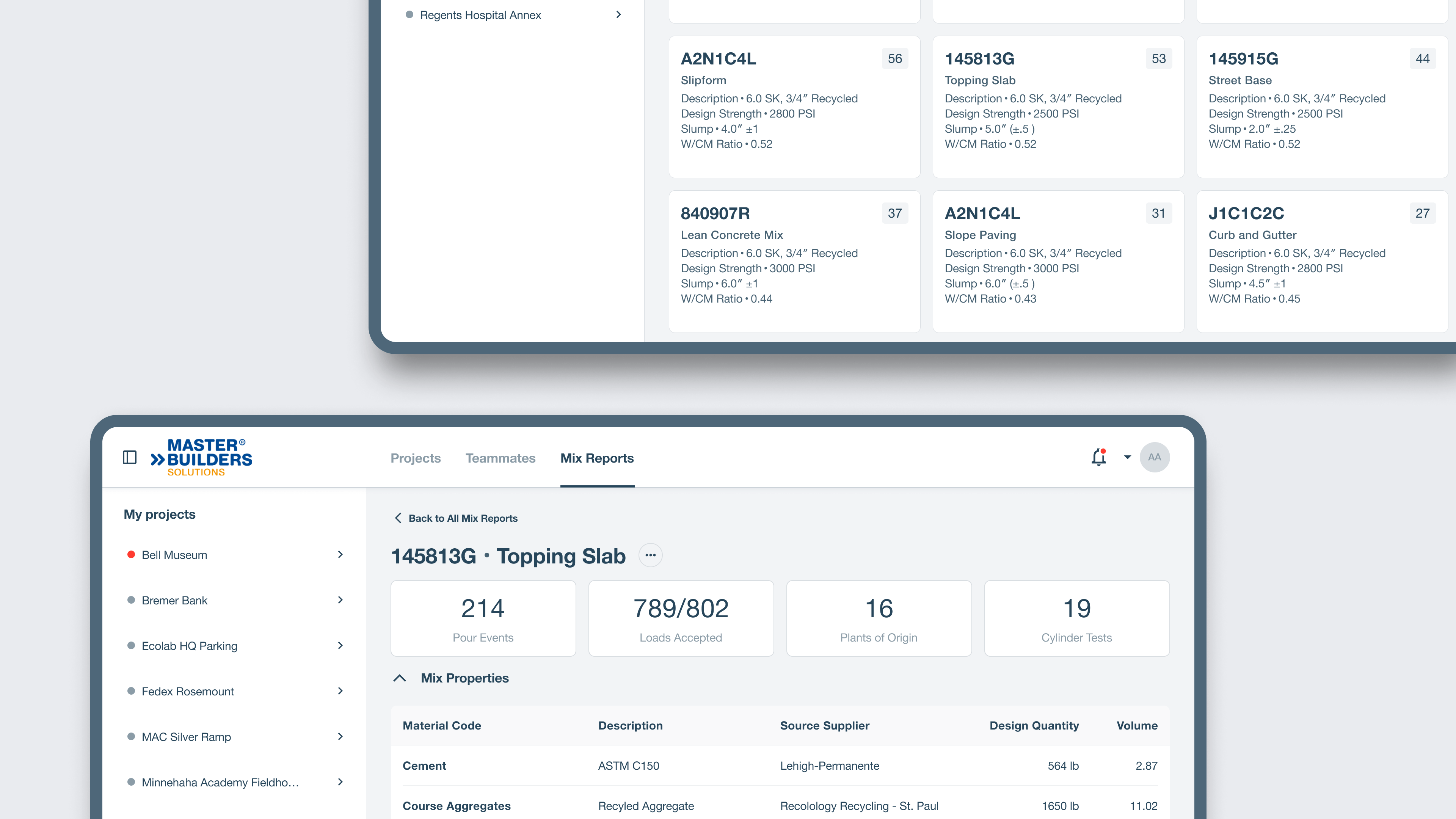
Outputs & Outcomes
Testing provided confidence to deliver a first generation product to Master Builders Solutions’ clients via native mobile (iOS & Android) apps and a desktop management portal.
Simple and Intuitive Interfaces
With a focus on intuitive usability, the experience was designed to require minimal training, making it accessible to all team members, regardless of their level of technical knowledge.
Personalized Experiences
Designed to address the specific needs of each user, ensuring they have access to the information and insights they need, when they need it. All team members are empowered to seamlessly engage and contribute to problem resolutions, creating a more efficient and cost-effective end-to-end process.
A Roadmap for Future Iterations
Next generation features were designed to integrate additional IoT data sources like on-site weather sensors to maximize the effectiveness of Master Builders Solutions' predictive AI product.